Corrective Action - the ISO 9001 Standard Requirements
Corrective action is meant to identify the root cause for the Nonconformity. Once the root cause is identified, motto of the company should be initiating an action to eliminate it: The corrective action. For implementation of successful corrective action, the stepping stone is an efficient documentation as only the documentation will help you to verify whether your corrective action was enough, effective and fruitful.
Objective of Corrective ActionBased on the requirements of the corrective action, the company needs to finalize on the objective. As required by ISO 9001, objectives of corrective action can be numerical, quantitative or qualitative. Additionally, according to the ISO 9001 requirements, all corrective actions should be limited in a timeframe. The time limit helps its reviewer to examine its effectiveness.

The Corrective Action Results - Requirements of ISO 9001
As per the ISO 9001, after implementing corrective action, you are supposed to observe and verify the corrective action taken and its objectives. Documentation at every step of implementation is an integral part of corrective action. When the action fails, opening a new one is recommended. Although this is not recommended by the ISO 9001 Standard but an unsuccessful corrective action indicates an open Nonconformity, which is forbidden by the ISO 9001 Standard.
Knowhow of Proper DocumentationFor successful documentation, make sure you are following the below given procedure:
- Document how the Nonconformity had been located
- The process investigation
- Action taken and
- The closing of the corrective action
Learn more about corrective action and learn how to be ISO 9001 compliant. For your entire CAPA related query, trust the best and world-class webinar provider - ComplianceOnline. We proudly recommend you to attend one of our webinars, conducted by the top-notch industry experts or you can also take the help of our CDs which, for your convenience, made in an easy-to-use format. So, what are waiting for? Come along with us and see all your CAPA issues to be eradicated in almost no time!
ComplianceOnline Trainings
|
Featured Products
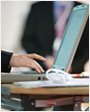
Price: $6800.00
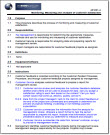
Price: $33.00


