Device Master Record - Document for Intended Employees
In order for employees to perform a job correctly, they should know exactly what is to be done and exactly how to do the work. The device master record also contains test and inspection procedures and data forms that are used to help determine and record what was done.
Documents that instruct people how to fabricate, assemble, mix, label, test, inspect, etc., or how to operate equipment should:
- be directed toward the needs of the employees who will be using them and not directed toward the drafts-person or designer;
- match the tools and equipment to be used;
- be correct, complete, and current; and
- depend on part numbers and basic drawings to transfer information rather than almost photographic type drawings.
The how to manufacture instructions should be adequate for use by the intended employees and correct for the intended operation. In the medium to large company, the instructions tend to be extensive technical (engineering) drawings and written procedures. In any company, particularly small manufacturers, the work instructions may take several forms as discussed below.
- Engineering drawings may be used if employees are trained to read and use them. Some of the how to information comes from employee training rather than from drawings.
- Assembly drawings may contain parts list and quality acceptance criteria. A separate quality acceptance test and/or inspection procedure is not always necessary. An example of an engineering drawing for assembling a handle is exhibited at the end of this chapter. This drawing also includes some of the quality acceptance criteria for evaluating the handle in Notes 1 and 2. The parts list for the handle is on the page after the assembly drawing. Some manufacturers that manufacture simple devices use large sheets of paper for assembly drawings and include the parts list on it. The combination drawing results in instant availability of the parts list and reduces the number of drawings to be controlled. An example of an engineering drawing for assembling a cable and the associated parts list follows the handle assembly drawings.
- view drawings are used when employees cannot read plan view engineering drawings. Exploded view drawings tend to be more "how to" than plan view drawings. Exploded view drawings are expensive to draft in some cases it may cost less to teach employees how to read and use ordinary plan view drawings.
- Step by step written procedures may be used to detail how to perform specific tasks with check off blanks to show that each specific task was performed. This type of procedure is commonly used for critical operations and where there is little or no visual indication of what has been done, such as for cleaning operations and for mixing chemicals.
The most commonly used aids are models or samples. There are two conditions that should be satisfied in order to use these aids. First, a written specification for the sample shall be contained in the device master record. Second, the sample should:
- adequately reflect the device master record specification;
- identified as an approved acceptable representative sample, which means it shall meet the company required workmanship standards; the sample need not be a working model if the nonworking condition is not misleading to employees being guided by the sample; and
- when appropriate, contain or be tagged with a drawing number, revision level, and control number (lot, serial, batch).
A card or tag as shown in the exhibits or an equivalent card may be used to identify and help control the use of samples of assemblies or finished devices. Such tags are usually covered by a clear plastic pouch and attached to the model or sample.
Samples and other aids such as photographs are subject to normal wear and tear in a production environment. Therefore, such aids should be adequately protected by a suitable means such as being located in a protected area, or covered by a protective pouch or container. Production aids should be periodically audited to make sure they continue to be suitable for the intended use. Section 820.100 contains requirements for corrective action. Corrective action may involve the use of samples, changes to the samples, or changes in the control of the samples.
Featured Products
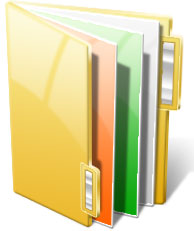
Price: $95.00
Quality System Regulation (QSR) - 21 CFR Part 820 - FDA Paperwork Act submission for QSR - FDA’s Quality System Inspection Technique (QSIT) Quality system procedures
FDA Quality Systems Regulations -Product Development Life Cycle -Design History File (DHF) -Device Master Record (DMR)- Device History Record (DHR)
Definition of Quality System Regulations (QSR)- Management Control-CAPA-Design Controls - Production and Process Controls (P&apm;PC)
Overview - key requirements - written procedures and training are required - internal audits