Medical Device Design Control: Design Output
As quoted in § 820.3(g), "Design output means the results of a design effort at each design phase and at the end of the total design effort. The finished design output is the basis for the device master record. The total finished design output consists of the device, its packaging and labeling, and the device master record."
Requirements: § 820.30(d) Design output
- Each manufacturer shall establish and maintain procedures for defining and documenting design output in terms that allow an adequate evaluation of conformance to design input requirements.
- Design output procedures shall contain or make reference to acceptance criteria and shall ensure that those design outputs that are essential for the proper functioning of the device are identified.
- Design output shall be documented, reviewed, and approved before release.
- The approval, including the date and signature of the individual(s) approving the output, shall be documented.
The quality system requirements for design output can be separated into two elements: Design output should be expressed in terms that allow adequate assessment of conformance to design input requirements and should identify the characteristics of the design that are crucial to the safety and proper functioning of the device. This raises two fundamental issues for developers:
- What constitutes design output?
- Are the form and content of the design output suitable?
Design output includes production specifications as well as descriptive materials which define and characterize the design.
Production Specifications:
Production specifications include drawings and documents used to procure components, fabricate, test, inspect, install, maintain, and service the device, such as the following:
- assembly drawings
- component and material specifications
- production and process specifications
- software machine code (e.g., diskette or master EPROM)
- work instructions
- quality assurance specifications and procedures
- installation and servicing procedures
- packaging and labeling specifications, including methods and processes used
In addition, as discussed in Section H (Design Transfer), production specifications may take on other forms. For example, some manufacturers produce assembly instructions on videotapes rather than written instructions. Similarly, a program diskette, used by a computer-aided milling machine to fabricate a part, would be considered a production specification. The videotape and the software on the program diskette are part of the device master record.
Other Descriptive Materials:
Other design output items might be produced which are necessary to establish conformance to design input requirements, but are not used in its production. For example, for each part which is fabricated by computer-aided machine, there should be an assembly drawing which specifies the dimensions and characteristics of the part. It is a part of the design output because it establishes the basis for the machine tool program used to fabricate the part. Other examples of design output include the following:
- the results of risk analysis
- software source code
- results of verification activities
- biocompatibility test results
- bioburden test results
Source:
www.fda.govRelated Training:
Design Controls Basics - From Design Inputs to Design Outputs and Effective Design TransferDesign Controls: What to know when it comes to FDA regulated industry?
Featured Products
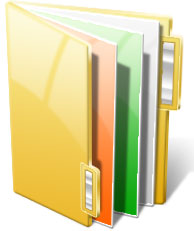
Price: $95.00
IND and IDE annual reports - Amending clinical protocols and informed consent – Format, Content, Editing, Submission of Documents
Meetings with FDA - Sample Size Considerations - Inclusion/Exclusion Criteria - End Points - Case Report Forms - Administrative Plan
The purpose of the IDE – FDA Expectations – preparation – recommended subject headings – content submission - follow up Usage in the clinical trial
Pre-IDE Meeting – Process- Submission preparation - presentation