Medical Device Design Verification and Validation
Verification and Validation are required as part of 21 CFR § 820.30. A review of recent FDA 483 observations indicates that a number of observations documented deficiencies in design verification and design validation. By learning from other firm’s mistakes and instituting a sound verification & validation strategy, along with proper verification and validation planning, these types of observations can be prevented.
Design Verification
As quoted in §820.3(aa), "Verification means confirmation by examination and provision of objective evidence that specified requirements have been fulfilled."
Requirements- § 820.30(f)
- Each manufacturer shall establish and maintain procedures for verifying the device design.
- Design verification shall confirm that the design output meets the design input requirements.
- The results of the design verification, including identification of the design, method(s), the date, and the individual(s) performing the verification, shall be documented in the Design History File.
Verification activities are conducted at all stages and levels of device design. The basis of verification is a three-pronged approach involving tests, inspections, and analyses. Any approach which establishes conformance with a design input requirement is an acceptable means of verifying the design with respect to that requirement. The nature of verification activities varies according to the type of design output.
Following are a few examples of verification methods and activities:
- Worst case analysis of an assembly to verify that components are derated properly and not subject to overstress during handling and use.
- Thermal analysis of an assembly to assure that internal or surface temperatures do not exceed specified limits.
- Fault tree analysis of a process or design.
- Failure modes and effects analysis.
- Package integrity tests.
- Biocompatibility testing of materials.
- Bioburden testing of products to be sterilized.
- Comparison of a design to a previous product having an established history of successful use.
Documentation of Verification Activities
One of the self-documenting verification method is the traceability matrix. This method is particularly useful when the design input and output are both documents; it also has great utility in software development. In the most common form of the traceability matrix, the input requirements are enumerated in a table, and references are provided to each section in the output documents (or software modules) which address or satisfy each input requirement.
Design Validation
As quoted in § 820.3(z), "Design Validation means establishing by objective evidence that device specifications conform with user needs and intended use(s)."
Requirements-§ 820.30(g)
- Each manufacturer shall establish and maintain procedures for validating the device design.
- Design validation shall be performed under defined operating conditions on initial production units, lots, or batches, or their equivalents.
- Design validation shall ensure that devices conform to defined user needs and intended uses and shall include testing of production units under actual or simulated use conditions.
- Design validation shall include software validation and risk analysis, where appropriate.
- The results of the design validation, including identification of the design, method(s), the date, and the individual(s) performing the validation, shall be documented in the Design History File.
Validation planning: Planning for validation should begin early in the design process. The performance characteristics that are to be assessed should be identified, and validation methods and acceptance criteria should be established. The validation plan should be reviewed for appropriateness, completeness, and to ensure that user needs and intended uses are addressed.
Validation review: Validation may expose deficiencies in the original assumptions concerning user needs and intended uses. A formal review process should be used to resolve any such deficiencies.
Validation methods: Many medical devices do not require clinical trials. However, all devices require clinical evaluation and should be tested in the actual or simulated use environment as a part of validation. This testing should involve devices which are manufactured using the same methods and procedures expected to be used for ongoing production. While testing is always a part of validation, additional validation methods are often used in conjunction with testing, including analysis and inspection methods, compilation of relevant scientific literature, provision of historical evidence that similar designs and/or materials are clinically safe, and full clinical investigations or clinical trials.
Validation documentation: Validation is a compilation of the results of all validation activities. For a complex design, the detailed results may be contained in a variety of separate documents and summarized in a validation report. Supporting information should be explicitly referenced in the validation report and either included as an appendix or available in the design history file.
Source:
www.fda.govRelated Training:
Understanding FDA Design Verification and Validation Requirements for Medical DevicesKey Considerations in Verification & Validation of Medical Devices
Featured Products
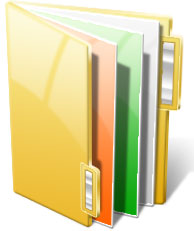
Price: $95.00
Quality System Regulation (QSR) - 21 CFR Part 820 - FDA Paperwork Act submission for QSR - FDA’s Quality System Inspection Technique (QSIT) Quality system procedures
FDA Quality Systems Regulations -Product Development Life Cycle -Design History File (DHF) -Device Master Record (DMR)- Device History Record (DHR)
Definition of Quality System Regulations (QSR)- Management Control-CAPA-Design Controls - Production and Process Controls (P&apm;PC)
Overview - key requirements - written procedures and training are required - internal audits