Medical Device Design Controls Guidance - Applicability
Design controls are a part of a comprehensive quality system that covers the life of a device. Design control begins with development and approval of design inputs, and includes the design of a device and the associated manufacturing processes.
Design control applies to all changes to the device or manufacturing process design, including those occurring long after a device has been introduced to the market. This includes evolutionary changes such as performance enhancements as well as revolutionary changes such as corrective actions resulting from the analysis of failed product.
The FDA guidance applies to the design of medical devices as well as the design of the associated manufacturing processes. The guidance document is applicable to new designs as well as modifications or improvements to existing device designs.
Quality System and Design Controls
In addition to procedures and work instructions necessary for the implementation of design controls, policies and procedures may also be needed for other determinants of device quality that should be considered during the design process. The need for policies and procedures for these factors is dependent upon the types of devices manufactured by a company and the risks associated with their use.
Example of topics for which policies and procedures may be appropriate are:
- risk management
- device reliability
- device durability
- device maintainability
- device serviceability
- human factors engineering
- software engineering
- use of standards
- configuration management
- compliance with regulatory requirements
- device evaluation (which may include third party product certification or approval)
- clinical evaluations
- document controls
- use of consultants
- use of subcontractors
- use of company historical data
The essential quality aspects and the regulatory requirements, such as safety, performance, and dependability of a product (whether hardware, software, services, or processed materials) are established during the design and development phase. Deficient design can be a major cause of quality problems.
The quality system requirements do not dictate the types of design process that a manufacturer must use. Manufacturers should use processes best suited to their needs. However, whatever the processes may be, it is important that the design controls are applied in an appropriate manner. This guidance document contains examples of how this might be achieved in a variety of situations.
Senior management needs to decide how the design function is to be managed and by whom. Senior management should also ensure that internal policies are established for design issues such as:
- assessing new product ideas
- training and retraining of design managers and design staff
- use of consultants
- evaluation of the design process
- product evaluation, including third party product certification and approvals
- patenting or other means of design protection
Source:
www.fda.govRelated Training:
Design Controls: What to Know When it Comes to FDA Regulated Industry?Understanding Design Controls for Medical Devices
Featured Products
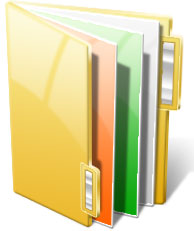
Price: $95.00
Quality System Regulation (QSR) - 21 CFR Part 820 - FDA Paperwork Act submission for QSR - FDA’s Quality System Inspection Technique (QSIT) Quality system procedures
FDA Quality Systems Regulations -Product Development Life Cycle -Design History File (DHF) -Device Master Record (DMR)- Device History Record (DHR)
Definition of Quality System Regulations (QSR)- Management Control-CAPA-Design Controls - Production and Process Controls (P&apm;PC)
Overview - key requirements - written procedures and training are required - internal audits