Your Shopping Cart
By using this site you agree to our use of cookies. Please refer to our privacy policy for more information. Close
Home
› Best Practices
Greening Supply Chain - Improving supply chain governance with sustainable supply chain model
- By: Ramesh Srinivasan, Manager MetricStream Inc
- Date: December 08, 2009
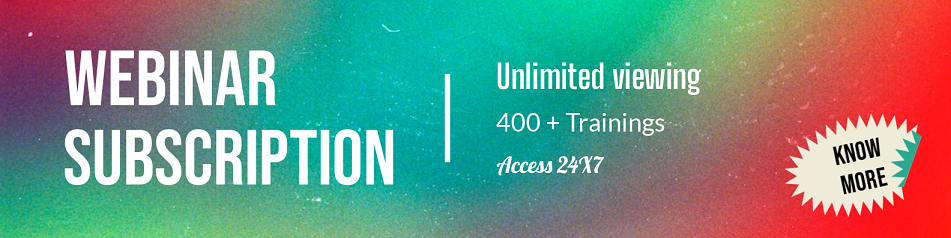
- Conventional costs - Material, labor, other expenses, and revenues that are commonly allocated to a product or process.
- Potentially Hidden - Expenses incurred by and benefits to the firm that are not typically traced to the responsible products or processes, e.g., supervisor salaries and safety training courses.
- Contingent - Potential liability or benefit that depends on the occurrence of a future event, e.g. potential occupational health and clean-up costs related to a spill of a hazardous substance.
- Image/Relationship - Costs/benefits related to the subjective perceptions of a firm’s stakeholders, e.g., a community group’s resistance to a plant expansion or an insurer’s concern about the lack of a formal environmental management system.
- External - Costs/benefits of a company’s impacts upon the environment and society that do not directly accrue to the business, e.g., the benefits of reduced traffic congestion from a company’s telecommuting program.
By taking into account the above costs, a company cannot only save potentially hidden expenses but also save the image of their product. For instance:
- Purchasing and Inbound: GM reduced its disposal costs by $12 million by establishing a reusable container program with its suppliers.
- Production: Commonwealth Edison, a major electric utility company, realized $25 million in financial benefits through more effective resource utilization.
- Outbound and Distribution: Andersen Corporation implemented several programs that reduced waste at its source and had internal rates of return (IRR) exceeding 50%.
-
Reverse Logistics: Public Service Electric and Gas Company saved more than $2 million in 1997 by streamlining its inventory process to avoid product obsolescence and disposal
Decision-Making Framework
While the potential benefits are significant, relatively few companies are pursuing the opportunity to improve their financial and environmental performance by explicitly addressing environmental costs. A clear, simple framework can help companies adopt Green Supply Management System.
By following the four-step framework companies can pinpoint and understand the costs and environmental impacts that result from materials management decisions.
Identify Costs: A systematic review of the facility or process is conducted to determine if and where significant environmental costs occur.
Determine Opportunities: The identified functional areas and processes are evaluated to determine which changes will likely yield significant cost savings and reduce environmental impacts. Potential changes are evaluated with criteria that can include the magnitude of potential cost improvement, the types of environmental burdens, and the barriers to change. This step yields a possible set of alternatives with significant potential for improving costs savings and reducing environmental impacts.
Calculate Benefits: Quantitative, and qualitative, analyses of the costs and benefits of a selected group of projects are conducted. Some of the analytical tools and methods used during this step are activity based costing approaches, net present value (NPV) calculations, and risk evaluations. The result is a
summary of the merits of the current process and any proposed alternatives.
Decide, Implement, and Monitor: First, a decision is made to continue with the status quo or to pursue a new approach. Financial benefits and/or environmental improvements then occur as changes are put into action. The new practices are institutionalized as information collection processes are integrated into the company’s materials resource planning (MRP II), enterprise resource planning (ERP) systems, and other information systems. After implementation, a periodic review and continuous improvement effort allows decision makers to evaluate their progress and pursue additional opportunities.
Compliance Trainings

Pregnancy in the Workplace: Strategies to Protect Your Organization from Pregnancy Discrimination Claims
By - Christopher W. Olmsted
On Demand Access Anytime
By - Christopher W. Olmsted
On Demand Access Anytime

How to Vet an IRB: Expose and Fix Problems Before They Threaten Your Trial
By - Madhavi Diwanji
On Demand Access Anytime
By - Madhavi Diwanji
On Demand Access Anytime

Compliance Standards
Best Sellers
- Add to Cart
- Add to Cart
- Add to Cart
- Add to Cart
- Add to Cart
- Add to Cart
- Add to Cart
- Add to Cart
-
By: Miles HutchinsonAdd to CartPrice: $249
- Add to Cart
- Add to Cart
- Add to Cart
- Add to Cart
- Add to Cart
- Add to Cart
-
San Francisco, CA | Aug 6-7, 2020
-
Virtual Seminar | Jul 16-17, 2020
-
Virtual Seminar | Jun 18-19, 2020
-
Los Angeles, CA | Aug 20-21, 2020
-
Virtual Seminar | Jul 16-17, 2020
-
Virtual Seminar | Jun 25-26, 2020
-
Virtual Seminar | Jun 10, 2020
-
Virtual Seminar | Jun 3-4, 2020
-
Virtual Seminar | Jul 6-7, 2020
-
San Francisco, CA | Oct 22-23, 2020
-
Virtual Seminar | Jul 9-10, 2020
-
Virtual Seminar | Jun 3-4, 2020
-
Virtual Seminar | June 3-4, 2020
-
Miami, FL | Jul 29-31, 2020
-
Virtual Seminar | Jun 17, 2020
-
Provider: ANSIAdd to CartPrice: $142
- Add to Cart
- Add to Cart
- Add to Cart
-
Provider: ANSIAdd to CartPrice: $120
-
Provider: ANSIAdd to CartPrice: $250
-
Provider: SEPTAdd to CartPrice: $299
- Add to Cart
-
Provider: Quality-Control-PlanAdd to CartPrice: $37
- Add to Cart
-
Provider: At-PQCAdd to CartPrice: $397
- Add to Cart
- Add to Cart
- Add to Cart
- Add to Cart
You Recently Viewed
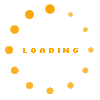