Best Practices for Change Control in a Pharmaceutical Manufacturing, Biologics, and Medical Device Environments
Insufficient change control is an area that features in the top 10 FDA 483 and Warning Letter citations issued to pharmaceutical manufacturing, biologics, and medical device industries. The FDA inspects change control very carefully during its audits. The FDA examines change control records to ensure changes have not negatively affected the facilities, equipment, processes, products, etc. A single deficient change can lead to serious adverse consequences, such as product launch with poor quality or even a product recall. System rectification efforts may cost money and time in case of a trend in deficient improvements.
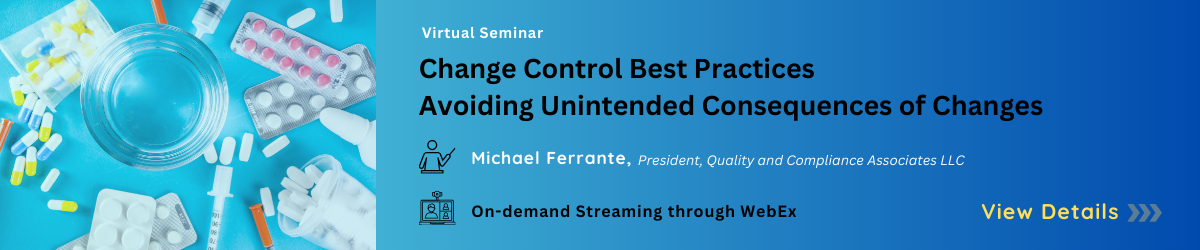
Regulatory Requirements for Change Control
FDA Change Control Expectations
- Change control is an inherent component of quality management in biologics, medical devices, and pharmaceutical industries.
- The FDA requires proper, strict change control processes so that when there are changes introduced, such changes do not have negative implications for the effectiveness, safety, or quality of the product.
- For the more significant changes, like those associated with the manufacturing process or specification, regulatory filings may be required, and even in some cases, regulatory approval before implementation could be mandated.
FDA Warning Letters
- One of the most common sources of FDA 483 violations and warning letters is poor change control.
- Some of the issues cited include inadequate risk assessments, lack of proper documentation for changes, and improper execution of changes.
Objectives of Change Controls
What is Change Control?
- A disciplined approach to any changes that are made in the process or product is called Change Control.
- It ensures that no unnecessary changes are made, all changes are well documented, and services are not disrupted for no reason.
Why / When Change Control?
The reason for change control is to maintain the integrity of the production process and its compliance with regulatory requirements. Changes should be controlled and documented so that in case something goes wrong, it does not affect the security and quality of the product that is being manufactured.
Physical Changes vs Document Changes
- This could involve physical changes to processes, materials, equipment, and facilities.
- Changes to documents include protocol amendments, specification changes, and other controlled documents.
Change Control Process
Change Control Process Model - Integrated Manufacturers
- In this model, the overall change control procedure is managed by the internal managers of integrated manufacturers.
- The managers have specialized teams that are concerned with risk assessments, proposals of change, and other implementation procedures.
Change Control Process Model - Sponsor Oversight of CMO Changes
- The changes proposed by the Contract Manufacturing Organizations have to be overseen by the sponsors.
- This involves verification and authorization of changes to ensure that it complies with the legal requirements.
Types of Changes under Change Control
Products, Materials, Suppliers, Processes, Facilities, Equipment, etc.
- Change control has to be utilized to administer any change introduced in equipment, facilities, suppliers, processes, materials or final products.
- This will ensure that the changes will not be subjected to safety and quality issues of the product.
Like-for-Like Changes
- Like-for-like changes are those where parts are replaced with exactly identical parts or similar ones.
- Even the minor changes should be documented and evaluated to ensure no surprise consequences occur.
Emergency Changes
- Emergency changes may have to be made against urgent issues.
- To ensure proper execution and acceptance, however, these changes should nonetheless follow a defined process.
Change Control: Yes or No?
- Not every change warrants formal change control.
- The decision of whether a change is significant enough to warrant formal documentation and scrutiny must be made.
Change Proposal
Components of a Change Proposal
A change proposal should therefore contain a detailed description of the change, the reason for change, and the impact that could be expected from the change. It must also deal with risks or regulatory issues.
Description of the Change
- Accurate and detailed enough to allow for full assessment
- Diagrams or drawings shall be provided together with the description, if necessary for clarification purposes of the change.
Change Proposal Documentation
A documented and agreed-upon assessment of this concept by the relevant parties, which at minimum includes regulatory affairs and quality assurance, and if appropriate any other departments that may be impacted by the change in the process.
Change Justification
Items to Include in the Justification of a Change
- The modification should be justified with valid arguments by data.
- It should outline why the change is being made, and how that will improve workflow or output.
Change Risk Assessment
- Conducting a comprehensive risk assessment is necessary in order to detect any consequences for product quality, safety, and compliance.
- To address hazards that have been identified, mitigation methods should be created.
Change Justification
The rationale has to be recorded and included to the change control logs. It should prove that the adjustment is both advantageous and required.
Develop a Comprehensive Change Execution Plan
Change Execution Plan Elements
The plan should outline all steps necessary to effect the change, including dates, responsibilities, and resources.
Change Execution Plan
- A clear plan ensures the smooth and successful execution of changes.
- Provisions for monitoring and evaluation of the effectiveness of the change should be included.
Evaluation of Proposed Change
SME Evaluations, by Functional Area
Subject matter experts (SMEs) from pertinent functional domains ought to evaluate the suggested modification. To make sure that all possible effects are taken into account, their involvement is essential.
Change Proposal Assessment
- The evaluation must to be comprehensive and impartial, taking into account every facet of the suggested modification.
- A review of the change reason, risk analysis, and execution strategy should be part of it.
Change Execution
How to Implement Changes
- Changes require adequate planning and coordination to be successfully implemented.
- Note any Interruptions; backup plans should be in place.
Proof of Change Closure
- Documentation is required for regulatory compliance that a change is indeed complete.
- All tasks executed, review results and approvals obtained should be documented as proof of completion.
Change Amendment / Cancellation
- It may prove necessary to modify or cancel a change in the light of new information or unforeseen difficulties.
- A written procedure should be established for dealing with such situations.
Implementing the Change
Planning the Introduction of Changes
- Relevant parties to be trained and informed regarding the change.
- The process of implementation shall be monitored to identify, and as promptly as possible address, problems encountered.
Verify the Effectiveness of Change
- Testing and monitoring to establish whether change is effective.
- Documenting the outcome and making any adjustment needed.
Change Control Documentation
Change Documentation Package Contents
- A documentation package of good change shall clearly include all relevant documents
- It comprises the change proposed, justification of the change, an assessment of the risks associated with the change, timeline for implementation, and evidence that it is completed.
Avoid these Common Pitfalls During the Change Control Process
The most prevalent ones are lack of stakeholder involvement, poor risk assessment, and poor documentation. These may be prevented by continuous improvement and implementation of the best practices.
Conclusion
In this way, effective change control is required to maintain product quality, safety, and regulatory compliance in a pharmaceutical manufacturing, biologics, and medical device environments. If organisations have followed the regulatory standards and best practises in managing change, they will be having reduced risks associated with inadequate change control.