The Fundamentals of Statistics for Quality Improvement
In business, decisions need to be taken based on data. Statistical thinking guides decision making based on the analysis of data. Many companies have a lot of data but don't know to turn their data into useful and actionable information. However, companies that make the best use of their available data achieve a competitive advantage by optimizing their operations and making superior decisions. It is all the more imperative for quality professionals to examine the best practices in statics for quality engineering to improve the performance of their current system.
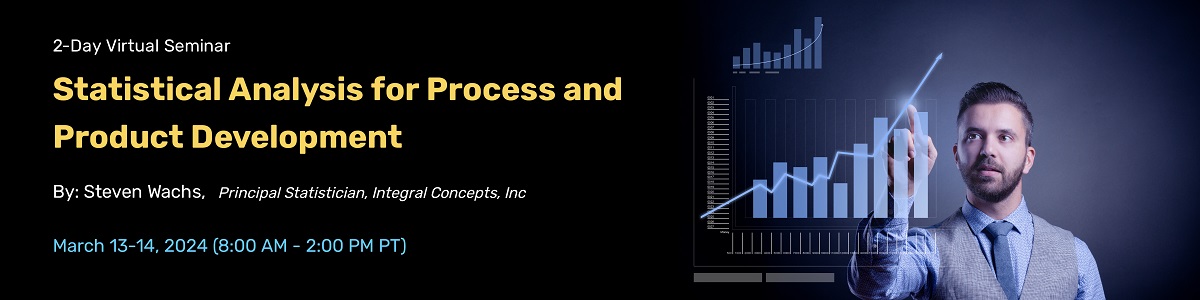
To focus on continual improvement, companies must make a shift from control-oriented management to statistical quality control. They must emphasize statistics rather than application. They must collect data and make faster decisions based on data
This article explains the basics of statistics and statistical methods for quality improvement to help you make substantive decisions.
- Random sampling: Randomization ensures independence among observations.
- Systematic samples: Systematic samples according to time or according to sequence
- Sampling by Rational Subgroup: a group of data that is logically homogenous; variation within the data can provide a measure for setting limits on the standard variation between subgroups.
- The type of sampling
- The personnel who will sample
- The persons for the use in-process inspection sample size
- The critical attributes to be inspected
- The location for the inspection
- Identify critical operations in the process where inspection might be needed.
- Identify critical product characteristics.
- Determine whether the critical product aspect is variable or attributable
- Choose the relevant process control chart from the many options available
- Determine and establish control limits and use a chart for ongoing monitoring and improvement.
- When you make changes to the process, update the limits
- To determine whether a process results in the product that meets the specifications
- To determine whether a process is in need of monitoring through the use of permanent process charts.
- Many companies fail to develop statistical thinking and culture.
- They fail to implement quality control in a substantive way and prefer form over substance.
- Some lack the knowledge about statistical tools, and so misapply them.
- Others have a general disdain for all things mathematics creates and that creates a barrier to the use of statistics.
- Cultural differences in a company sometimes make the use of statistics for quality improvement a bottleneck.
- Statistical experts find it difficult to communicate with managerial generalists.
- Lack of understanding of statistical methods
- Lack of proper education in statistics
- Lack of patience in collecting data
- Fear of violating critical statistical assumptions
- Some people don't understand random variation
The statistical fundamentals
Statistics are tools that help in analyzing data, making summaries, drawing inferences, and generalizing from the data. Statistics are highly crucial in the field of quality. Learning how to develop different statistical charts and statistical techniques is crucial. However, learning how to apply those techniques in a way that will document and stimulate continual improvement of the organization is even more important.
Central to quality improvement is statistical thinking. Statistical thinking is a skill that is displayed by the ability to make decisions based on data. Such thinking is based on three concepts as shown in the figure below:
Three concepts of statistical thinking
Process variation
All processes display variation. There is some variation that can be controlled and others that cannot be controlled. If the variation is too high, the process parts will not fit in properly, the product will be defective, and the company's reputation for quality will be at stake if corrective actions are not taken.
There are two types of variations that occur commonly viz. random and nonrandom variation.
Process stability
When a process performs consistently over time, then the process is considered to be stable or in control. Process stability refers to the steadiness of the process with regard to critical process characteristics such as the average value of a key dimension or the variation in that key dimension.
The process stability is determined by using process charts. Process charts are charts that signal the process personnel when a nonrandom variation occurs in a process.
Sampling methods
Data are gathered in samples to ensure the stability of the process. Sampling methods are preferred and are better established because they are cost-effective, less intrusive, fast, and their destructive testing features. They also let the user frame the sample.
Considerations for Planning for inspection
Process control charts
Process control chart definition
"A control chart is a statistical tool used to distinguish between variation in a process resulting from common causes and variation resulting from special causes. It presents a graphic display of process stability or instability over time." (Air University)
The main purpose of a process control chart is to indicate when production processes might have changed sufficiently to affect product quality. If the chart shows that the quality of the product has deteriorated, it is an indication to take corrective actions.
General guidelines for developing process charts
Process stability and capability
When a process is stabilized, the immediate next step is to ensure the process is capable. Process capability is the ability of the process to produce the desired product. The six sigma is one such program that results in highly capable processes.
Capability studies are conducted for two reasons:
There are many forms used in the statistical methods for quality improvement:
Hypothesis testing: A statistical method for making statistical decisions using experimental data. Hypothesis Testing is basically an assumption that can be made about the population criteria.
Regression analysis: A study to understand the relationship between two or more variables.
Statistical process control: An industry-standard methodology for measuring and controlling quality during the manufacturing process.
Design and analysis experiments: Planning, directing, examining and interpreting controlled tests to evaluate the factors that may influence a response variable.
Why some companies fail with statistics