The top 5 Issues with the Creation, Management, and Implementation of Standard Operating Procedures (SOPs) and how to resolve them
Are you a senior manager responsible for process improvements in your organization? If so, developing a process that minimizes human errors is a crucial part of your job.
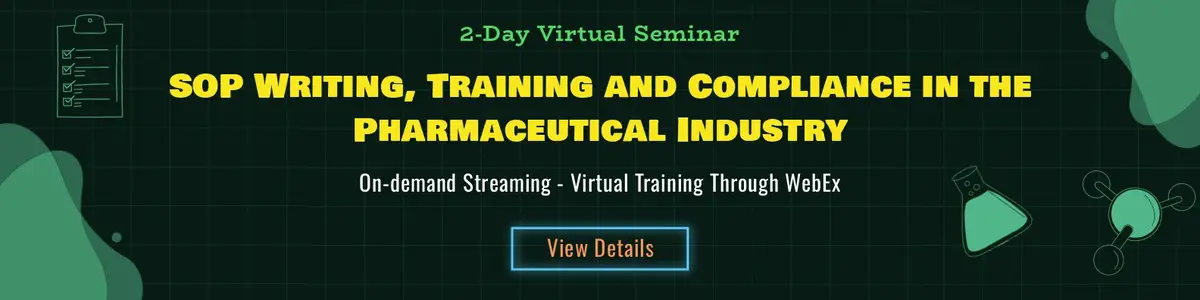
The experience of many companies demonstrates that human error is a key contributor to operating inefficiencies and significant business losses. However, they are often caused due to process issues, they are within your power to control and change. By creating well-written SOPs, most errors can be prevented. The advantages of preventing human errors by creating effective SOPS are illustrated below:
Most drug development, testing, manufacturing, and marketing programs have SOPs and appreciate their importance. However, there is a lack of proper understanding of many facets of SOP creation, maintenance, training, and organization resulting in stacks of errors with regulatory compliance identified during FDA audits. This article presents some of the most common issues with the creation, management, and implementation of SOPs
Inadequate SOPs
- Section 211.22(d)-Responsibilities and procedures of the quality control unit;
- Section 211.56(b)-Sanitation procedures
- Section 211.56(c)-Use of suitable rodenticides, insecticides, fungicides, sanitizing agents;
- Section 211.67(b)-Cleaning and maintenance of equipment;
- Section 211.68(a)-Proper performance of automatic, mechanical, and electronic equipment;
- Section 211.80(a)-Receipt, identification, storage, handling, sampling, testing, and approval or rejection of components and drug product containers or closures;
- Section 211.94(d)-Standards or specifications, methods of testing, and methods of cleaning, sterilizing, and processing to remove pyrogenic properties for drug product containers and closures;
- Section 211.100(a)-Production and process control;
- Section 211.110(a)-Sampling and testing of in-process materials and drug products;
- Section 211.113(a)-Prevention of objectionable microorganisms in drug products not required to be sterile;
- Section 211.113(b)-Prevention of microbiological contamination of drug products purporting to be sterile, including validation of any sterilization process;
- Section 211.115(a)-System for reprocessing batches that do not conform to standards or specifications, to insure that reprocessed batches conform with all established standards, specifications, and characteristics;
- Section 211.122(a)-Receipt, identification, storage, handling, sampling, examination and/or testing of labeling and packaging materials;
- Section 211.125(f)-Control procedures for the issuance of labeling;
- Section 211.130-Packaging and label operations, prevention of mixup and cross contamination, identification and handling of filed drug product containers that are set aside and held in unlabeled condition, and identification of the drug product with a lot or control number that permits determination of the history of the manufacture and control of the batch;
- Section 211.142-Warehousing;
- Section 211.150-Distribution of drug products;
- Section 211.160-Laboratory controls;
- Section 211.165(c)-Testing and release for distribution;
- Section 211.166(a)-Stability testing;
- Section 211.167-Special testing requirements;
- Section 211.180(f)-Notification of responsible officials of investigations, recalls, reports of inspectional observations, and any regulatory actions relating to good manufacturing practice;
- Section 211.198(a)-Written and oral complaint procedures, including quality involving specifications failures, and serious and unexpected adverse drug experiences;
- Section 211.204-Holding, testing, and reprocessing of returned drug products; and
- Section 211.208-Drug product salvaging.
Noncompliance with the Company's own SOPs
Poorly written SOPs
Lack of proper maintenance of SOPs
- Failure to incorporate the procedural changes
- Failure to include the history of changes - properly annotating the SOP with the version number, effective dates and categorization is important.
- Lack of summary of changes from previous to current changes
- Lack of proper formatting, pagination, headers, and footers on all pages, and other measures
- Lack of formal definitions for updating SOPs in a written document. It is crucial to document the practices for revising existing SOPs, creating new ones and training, retraining and authorizing staff in all processes
- Lack of Proper access for relevant staff to SOPs whenever they need to reference them.
- Lack of proper control and limit access to the SOPs - Only the authorized personnel should be given access
Lack of extensive SOP training
- Administering quizzes
- Assigning mentors
- Conducting performance reviews and document it
- Using checklists and other forms to monitor tasks and ensure compliance
- Signing with the date on any documentation associated with SOPs
Creating SOPs is a regulatory requirement. The FDA, ISO, and ICH guidelines frequently mention requirements for SOPs. Many parts of Title 21 in the Code of Federal Regulations (CFR), describe the requirements. Below is one such:
21 CFR Sec. 211.100: "There shall be written procedures for production and process control designed to assure that the drug products have the identity, strength, quality, and purity they purport or are represented to possess
These written procedures shall be drafted, reviewed, and approved by the appropriate organizational units and reviewed and approved by the quality control unit
Written production and process control procedures shall be followed in the execution of the various production and process control functions and shall be documented at the time of performance
Any deviation from the written procedures shall be recorded and justified."
The Federal Register (Vol. 76, No. 188 / Wednesday, September 28, 2011) presents a summary of the SOPs required by 21 CFR Part 211. 25 key process operations that need SOPs include:
Although the regulatory bodies require the creation of SOPs, they do not provide guidance on the format or specific style and content. Companies can design them in a manner they discern is best to ensure process control and compliance. After an organization defines its SOPs, it should comply with them. SOPs are written procedures that define how an activity is performed from the start to completion. It is a way to express the organization's commitments made regarding the conduct and process. Organizations are required to show compliance with those processes. Most audit findings can be ascribed to noncompliance with the Company's own procedures.
Following a set of written procedures may appear simple, however, if the procedures are poorly written, or are outdated, deviations in practice occur. These errors are often identified during FDA audits. However, organizations can gain the FDA's approval by learning how to write clear, effective SOPs that staff can easily adapt.
Procedures change with time and experience. However, many companies fail to formalize the procedural changes in the current version of their SOPs. Some of the common maintenance issues include
Having well-written SOPs doesn't mean much if staff are not adequately trained. The management must ensure that all concerned personnel read and understand the SOPs for which they are responsible. Most Auditors are highly interested in key training records. They also gauge the employee's understanding of the processes by asking them to explain what's in the SOP and show the performance of the task. Ways to evaluate employee conformance to SOPs include:
How to resolve the issues
- Have a procedure in place for determining what procedures or processes need to be documented
- Understand the compliance regulations well
- Be knowledgeable about the activity
- Be knowledgeable with the internal structure
- Be subject-matter expert who actually performs the work or uses the process
- Follow a team approach, especially for multi-tasked processes where the experiences of a number of individuals are critical
- Review and validate the SOPs by one or more individuals with appropriate training and experience with the process
- Test draft SOPs by individuals other than the original writer before finalizing
- Have the SOPs approved as per the Organization's Quality management plan
- Review SOPs on a periodic basis
- When there is a process change, update and re-approve SOPs
- Maintain a master list of SOPs indicating the SOP number, version number, date of issuance, title, author, status, organizational division, branch, section, and any historical information regarding past versions
Attend the webinar 'How to write SOP's that Avoid Human Error to understand human behavior and the psychology of error as well as identify exactly where the instructions' weaknesses are, so procedures can be human engineered, improved and/or fixed. This webinar offers practical approaches to address writing rules to reduce the likelihood of procedures.
The instructor, Ginette Collazo, PH.D, is a human error and human behavior expert. She has spent more than 15 years in technical training, organizational development and human reliability areas. She has worked with Bristol-Myers Squibb, Johnson & Johnson, Schering-Plough, Wyeth, and has been a consultant with major firms like Abbott, Johnson & Johnson, Perrigo, among many others. She has also implemented human error reduction programs and technology in many small and mid-sized drug and device companies. An active researcher in specialized studies related to human reliability, she is the author of numerous publications on these topics.