Your Shopping Cart
By using this site you agree to our use of cookies. Please refer to our privacy policy for more information. Close
ISO/IEC 17025 – Applicability, Use and Summary of Requirements
- By: Staff Editor
- Date: September 02, 2011
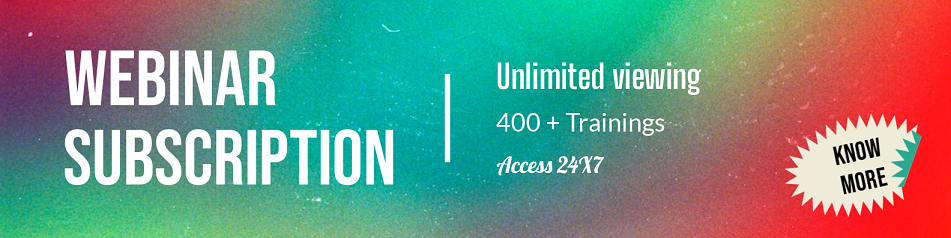
Applicability
The ISO/IEC 17025 applies to all organizations performing tests and/or calibrations. These include, for example, first-, second- and third-party laboratories, and laboratories where testing and/or calibration forms part of inspection and product certification.
ISO/IEC 17025 is applicable to all laboratories regardless of:
- The number of personnel or
- The extent of the scope of testing and/or calibration activities.
If a laboratory does not undertake one or more of the activities covered by ISO/IEC 17025, then the clauses pertaining to those activities don’t apply.
To understand the full requirements of the ISO/IEC 17025, get the standard and related manuals and checklists from the ComplianceOnline store:
Or attend any of the following ComplianceOnline webinars:
|
||
Use
This standard, the latest of which was released in 2005 is to be used by laboratories in developing their management system for quality, administrative and technical operations.
Laboratory customers, regulatory authorities and accreditation bodies may also use it in confirming or recognizing the competence of laboratories.
However, the ISO/IEC 17025 is not intended to be used as the basis for certification of laboratories.
This standard doesn’t cover the regulatory and safety requirements for laboratories.
Content
The ISO/IEC 17025 includes the following:
- Scope
- Normative references
- Terms and definitions
- Management requirements
- Technical requirements
Management Requirements
The Management Requirements section of the ISO/IEC 17025 standard is divided into 15 chapters:
Organization | Roles and responsibilities of key personnel, laboratory and management should be defined |
Management system | Management system should be implemented, maintained and reviewed for improvements |
Document control | The management system should be documented – requires documentation control and properly defined processes |
Review of requests, tenders and contracts | The requirements of requests, tenders and contracts should be properly defined, reviewed, documented and understood by lab management |
Subcontracting of tests and calibrations | Those testing and calibration activities sub-contracted to third parties have to follow the same quality standards and competence requirements |
Purchasing services and supplies | Suppliers have to be evaluated to ensure quality is maintained and these processes have to be properly documented |
Service to the customer | Customers’ requests, input and feedback have to be handled with a proper system or mechanism and have to be documented |
Complaints | Customer complaints should be documented, evaluated and there should be a proper follow-up process |
Control of non-conforming testing and/or calibration work | Non-conforming testing and calibration results should be followed up and corrective actions should be performed |
Continuous improvement | Lab management improvements should be implemented after analyzing audit reports, data, customer complaints and feedback, corrective and preventive actions and management reviews |
Corrective action | The root cause of nonconforming work or deviations from laboratory and management procedures should be identified and appropriate corrective actions applied and monitored. |
Preventive action | When potential sources of nonconformities have been identified, preventive actions should be initiated |
Control of records | All records in a laboratory need:
|
Internal audits | Internal audits have to be carried out to ensure that the laboratory complies with ISO/IEC 17025 requirements |
Management reviews | Management reviews have to be carried out to ensure that systems are stable and effective, especially the quality system and testing and calibration procedures |
Technical requirements
The technical requirements clause in this standard includes the following ten chapters:
General |
|
Personnel |
|
Accommodation and environmental conditions | The calibration and test areas should not be affected by an adverse physical environment – optimum conditions have to be maintained at all times |
Test and calibration methods and method validation | Test and calibration methods have to be kept up to date and validated in order to achieve the best possible results |
Equipment | Equipment has to be properly maintained and performing well in order to get the best and most accurate results |
Measurement traceability | All measurements on all equipments have to be ideally traceable to the International System of Units (SI) |
Sampling | Statistically relevant, representative samples have to be taken and procedures properly documented |
Handling test and calibration items |
|
Assuring quality of test and calibration results | Quality control samples should be analyzed regularly and checks implemented |
Reporting of results | Results should be recorded accurately and clearly, plus conform to the result reporting requirements in the standard |
Compliance Trainings

Acceptance Sampling Plans for Process Validation and Production Lot Monitoring
By - Steven Wachs
On Demand Access Anytime
By - Steven Wachs
On Demand Access Anytime

3-Hr Virtual Training: Introduction to Design of Experiments
By - Steven Wachs
On Demand Access Anytime
By - Steven Wachs
On Demand Access Anytime


Compliance Standards
Best Sellers
- Add to Cart
- Add to Cart
- Add to Cart
- Add to Cart
- Add to Cart
- Add to Cart
- Add to Cart
- Add to Cart
-
By: Miles HutchinsonAdd to CartPrice: $249
- Add to Cart
- Add to Cart
- Add to Cart
- Add to Cart
- Add to Cart
- Add to Cart
-
San Francisco, CA | Aug 6-7, 2020
-
Virtual Seminar | Jul 16-17, 2020
-
Virtual Seminar | Jun 18-19, 2020
-
Los Angeles, CA | Aug 20-21, 2020
-
Virtual Seminar | Jul 16-17, 2020
-
Virtual Seminar | Jun 25-26, 2020
-
Virtual Seminar | Jun 10, 2020
-
Virtual Seminar | Jun 3-4, 2020
-
Virtual Seminar | Jul 6-7, 2020
-
San Francisco, CA | Oct 22-23, 2020
-
Virtual Seminar | Jul 9-10, 2020
-
Virtual Seminar | Jun 3-4, 2020
-
Virtual Seminar | June 3-4, 2020
-
Miami, FL | Jul 29-31, 2020
-
Virtual Seminar | Jun 17, 2020
-
Provider: ANSIAdd to CartPrice: $142
- Add to Cart
- Add to Cart
- Add to Cart
-
Provider: ANSIAdd to CartPrice: $120
-
Provider: ANSIAdd to CartPrice: $250
-
Provider: SEPTAdd to CartPrice: $299
- Add to Cart
-
Provider: Quality-Control-PlanAdd to CartPrice: $37
- Add to Cart
-
Provider: At-PQCAdd to CartPrice: $397
- Add to Cart
- Add to Cart
- Add to Cart
- Add to Cart
You Recently Viewed
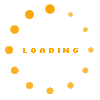