Your Shopping Cart
By using this site you agree to our use of cookies. Please refer to our privacy policy for more information. Close
Home
› Best Practices
OSHA’s New Laboratory Safety Guidance – Overview and Summary of Requirements
- By: Staff Editor
- Date: October 28, 2011
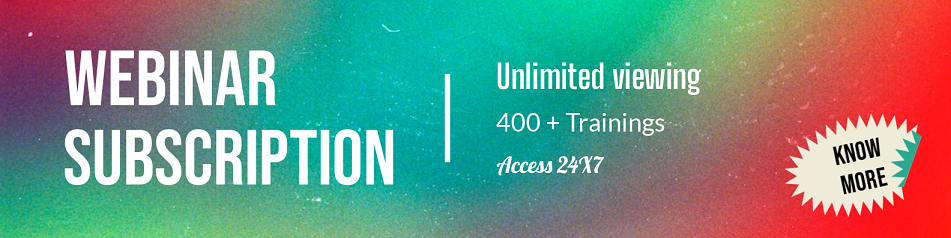
OSHA’s new Laboratory Safety Guidance document, released on October 13, 2011, details how to prevent hazards such as electrical, fire, explosions and falls in laboratories. The guidance describes preventive methods that employers can use, such as safety plans, worker training, engineering controls and personal protective equipment.
The new guidance also includes fact sheets that each focus on specific hazards specific to laboratory environments.
OSHA decided to updates its guidance as there has been an increase in the number of laboratory incidents resulting in fatalities and injuries caused by fires, explosions and equipment.
In a statement, Assistant Secretary of Labor for Occupational Safety and Health David Michaels, said, “The chemicals and equipment that laboratory workers use present a number of serious, sometimes life-threatening hazards. These educational materials will help employers identify hazards and measures to ensure safe and healthful conditions for their workers and promote a robust safety culture in the workplace”
Overview of OSHA Laboratory Safety Guidance
The new OSHA Laboratory Safety Guidance describes the ways to prevent and deal with the following laboratory environment hazards:
- Chemical
- Biological
- Physical and others
- Safety
Standards used in the guidance document
The following OSHA standards are used as the framework for the Laboratory Safety Guidance:
- The Occupational Exposure to Hazardous Chemicals in Laboratories standard (29 CFR 1910.1450)
- The Hazard Communication standard (29 CFR 1910.1200)
- The Bloodborne Pathogens standard (29 CFR 1910.1030)
- The Personal Protective Equipment (PPE) standard (29 CFR 1910.132)
- The Eye and Face Protection standard (29 CFR 1910.133)
- The Respiratory Protection standard (29 CFR 1910.134)
- The Hand Protection standard (29 CFR 1910.138)
- The Control of Hazardous Energy standard (29 CFR 1910.147)
Need to comply with OSHA standards in the workplace? Attend any of the following ComplianceOnline webinars:
|
||
Hierarchy of controls for laboratory hazards
According to the OSHA guidance document, in laboratories, the following hierarchy (from most effective to least effective) of controls should ideally be followed in order to protect workers:
- Engineering controls – Involve making changes to the work environment to reduce work-related hazards
- Administrative controls – Modify workers’ tasks and schedules to reduce exposure to work-related hazards
- Work practices – Procedures for safe and proper work that reduces duration, frequency and intensity of hazard exposure.
- Personal protective equipment (PPE) – Protective gear needed to keep workers safe while performing their jobs.
Employers must evaluate their particular workplace to develop a plan for protecting their workers that may combine both immediate actions as well as longer term solutions.
Chemical Hazards
Hazardous chemicals present physical and health threats to workers in clinical, industrial and academic laboratories. These chemicals include:
- Cancer-causing agents (carcinogens),
- Toxins (e.g., those affecting the liver, kidney, and nervous system),
- Irritants, corrosives, sensitizers, as well as agents that act on the blood system or damage the lungs, skin, eyes, or mucous membranes.
According to OSHA’s Laboratory Standard, chemical hazards should be handled by:
- Hazard identification - Each laboratory must identify which hazardous chemicals will be encountered by its workers.
- Chemical Hygiene Plan (CHP)- The purpose of the CHP is to provide guidelines for prudent practices and procedures for the use of chemicals in the laboratory.
- Information and training - Laboratory workers must be provided with information and training relevant to the hazards of the chemicals present in their laboratory.
- Exposure monitoring – The employer must ensure that workers’ exposures to OSHA-regulated substances do not exceed the permissible exposure limits (PEL).
- Medical consultation and examinations – Employers must provide all workers opportunities to medical attention or consultations from a licensed physician.
Biological Hazards
The Laboratory Safety Guidance from OSHA describes the following biological hazards that laboratory workers face:
- Biological Agents (other than Bloodborne Pathogens) and Biological Toxins - Employers can use the list given in the guidance as a starting point for technical and regulatory information about some of the most virulent and prevalent biological agents and toxins.
- Bloodborne Pathogens - Employers are subject to OSHA’s Bloodborne Pathogen (BBP) standard if they have workers whose jobs put them at reasonable risk of coming into contact with blood or other potentially infectious materials (OPIM).
- Research Animals - All procedures on animals should be performed by properly trained personnel. By using safe work practices and appropriate PPE, 29 CFR 1910.132(a), workers can minimize the likelihood that they will be bitten, scratched, and/or exposed to animal body fluids and tissues.
The Laboratory Safety Guidance details ways to deal with each of the above biological hazards.
The Guidance also recommend the use of Biological Safety Cabinets or BSCs, which when used in conjunction with good microbiological techniques, provide an effective containment system for safe manipulation of moderate and high-risk infectious agents [Biosafety Level 2 (BSL 2) and 3 (BSL 3) agents]. BSCs protect laboratory workers and the immediate environment from infectious aerosols generated within the cabinet.
Physical Hazards and Others
Laboratory workers can be exposed to a number of physical hazards including:
- Ergonomic - By becoming familiar with how to control laboratory ergonomics-related risk factors, employers can reduce chances for occupational injuries while improving worker comfort, productivity, and job satisfaction.
- Ionizing radiation - The OSHA Ionizing Radiation standard requires precautionary measures and personnel monitoring for workers who are likely to be exposed to radiation hazards.
- Non-ionizing radiation – OSHA provides regulatory guidelines on how to deal with hazards from non-ionizing radiation, which includes the spectrum of ultraviolet (UV), visible light, infrared (IR), microwave (MW), radio frequency (RF), and extremely low frequency (ELF).
- Noise hazards - OSHA’s Occupational Noise Exposure standard, 29 CFR 1910.95, requires employers to develop and implement a hearing conservation program that includes the use of PPE (e.g., hearing protectors), if workers are exposed to a time-weighted average (TWA) of ≥ 85 dBA over an 8-hour work shift. In addition, when workers are exposed to noise levels ≥ 85 dBA, the employer must develop a monitoring program to assess noise levels.
Safety Hazards
The Laboratory Safety Guidance describes how to deal with the following safety hazards to laboratory workers:
- Autoclaves and Sterilizers - Workers should be trained to recognize the potential for exposure to burns or cuts that can occur from handling or sorting hot sterilized items or sharp instruments when removing them from autoclaves/sterilizers or from steam lines that service the autoclaves.
- Centrifuges
- Employers should instruct workers when centrifuging infectious materials that they should wait 10 minutes after the centrifuge rotor has stopped before opening the lid.
- Workers should also be trained to use appropriate decontamination and cleanup procedures for the materials being centrifuged if a spill occurs and to report all accidents to their supervisor immediately.
- Compressed Gases – Compressed gases should be stored, handled and used in accordance with OSHA’s Compressed Gases standard (29 CFR 1910.101) and Pamphlet P-1-1965 from the Compressed Gas Association:
- All cylinders whether empty or full must be stored upright.
- Secure cylinders of compressed gases. Cylinders should never be dropped or allowed to strike each other with force.
- Transport compressed gas cylinders with protective caps in place and do not roll or drag the cylinders.
- Cryogens and Dry Ice – To protect laboratory workers, employers should:
- Conduct a safety analysis and review for all cryogenic facilities,
- Give cryogenic safety and operational training for relevant workers,
- Ensure appropriate maintenance of cryogenic systems in their original working order, i.e., the condition in which the system was approved for use, and
- Ensure upkeep of inspection schedules and records.
- Electrical – Employers should comply with the requirements outlined in OSHA Standards 1910 Subpart S-Electrical
- Fire – Employers should implement proper procedures and training to prevent accidental fires and also train lab workers on dealing with fire emergencies
- Lockout/Tagout – OSHA’s Lockout/Tagout standard establishes basic requirements involved in locking and/or tagging equipment while installation, maintenance, testing, repair or construction operations are in progress.
- Trips, Slips and Falls – OSHA standard 29 CFR 1910 Subpart D – Walking-Working Surfaces, Subpart E – Means of Egress, and Subpart J - General environmental controls gives outlines safety procedures to deal with hazards that could result in trips, slips and fall that may injure lab workers.
Additional Resources
Compliance Trainings

Pregnancy in the Workplace: Strategies to Protect Your Organization from Pregnancy Discrimination Claims
By - Christopher W. Olmsted
On Demand Access Anytime
By - Christopher W. Olmsted
On Demand Access Anytime

How to Vet an IRB: Expose and Fix Problems Before They Threaten Your Trial
By - Madhavi Diwanji
On Demand Access Anytime
By - Madhavi Diwanji
On Demand Access Anytime

Compliance Standards
Best Sellers
- Add to Cart
- Add to Cart
- Add to Cart
- Add to Cart
- Add to Cart
- Add to Cart
- Add to Cart
- Add to Cart
-
By: Miles HutchinsonAdd to CartPrice: $249
- Add to Cart
- Add to Cart
- Add to Cart
- Add to Cart
- Add to Cart
- Add to Cart
-
San Francisco, CA | Aug 6-7, 2020
-
Virtual Seminar | Jul 16-17, 2020
-
Virtual Seminar | Jun 18-19, 2020
-
Los Angeles, CA | Aug 20-21, 2020
-
Virtual Seminar | Jul 16-17, 2020
-
Virtual Seminar | Jun 25-26, 2020
-
Virtual Seminar | Jun 10, 2020
-
Virtual Seminar | Jun 3-4, 2020
-
Virtual Seminar | Jul 6-7, 2020
-
San Francisco, CA | Oct 22-23, 2020
-
Virtual Seminar | Jul 9-10, 2020
-
Virtual Seminar | Jun 3-4, 2020
-
Virtual Seminar | June 3-4, 2020
-
Miami, FL | Jul 29-31, 2020
-
Virtual Seminar | Jun 17, 2020
-
Provider: ANSIAdd to CartPrice: $142
- Add to Cart
- Add to Cart
- Add to Cart
-
Provider: ANSIAdd to CartPrice: $120
-
Provider: ANSIAdd to CartPrice: $250
-
Provider: SEPTAdd to CartPrice: $299
- Add to Cart
-
Provider: Quality-Control-PlanAdd to CartPrice: $37
- Add to Cart
-
Provider: At-PQCAdd to CartPrice: $397
- Add to Cart
- Add to Cart
- Add to Cart
- Add to Cart
You Recently Viewed
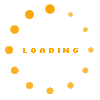