Your Shopping Cart
By using this site you agree to our use of cookies. Please refer to our privacy policy for more information. Close
Home
› Best Practices
OSHA’s Safety and Health Achievement Recognition Program – What are Best Practices that Small Businesses Can Follow?
- By: Staff Editor
- Date: February 03, 2012
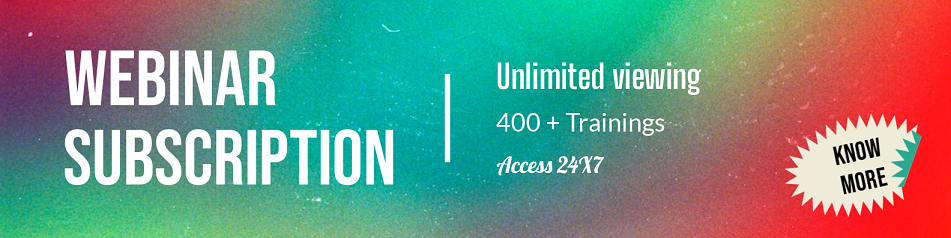
OSHA’s acceptance or recognition of the worksite of a small business / small employer into SHARP (Safety and Health Achievement Recognition Program) confers a certain status on the small business / small employer concerned. Besides, the recognized small business / small employer gains exemption from OSHA-programmed inspections as long as the SHARP certification remains valid. To be specific, the small business / small employer gains an exemption from OSHA programmed inspections for up to 2 years, and subsequent renewal for up to 3 years. However, participation in SHARP does not eliminate the responsibilities of owners or rights of workers under the Occupational Safety and Health Act. But, formal complaints, fatality, imminent danger situations and any other significant events as directed by the Assistant Secretary of OSHA can still trigger an OSHA enforcement inspection at SHARP sites. If the small business / small employer concerned follows the best practices consistently and dedicatedly, it can stand out among its business peers as a model for worksite safety and health.
OSHA’s 1989 Safety and Health Program Management Guidelines
- To participate in SHARP, the small business / small employer begins by seeking a comprehensive consultation visit from its on-site consultation office by indicating therein the name of the relevant State for the consultation project in its area and the address of the project office. This leads to a comprehensive hazard identification survey.
- It should necessarily involve its employees in the consultation process
- It should correct all hazards identified by the consultant.
- It should formulate, implement and maintain a safety and health management system that, at a minimum, complies with OSHA’s 1989 Safety and Health Program Management Guidelines.
- The guidelines represent the main ideas or facts from the larger amount of information on applied safety and health management practices followed by employers successful in protecting the safety and health of their employees.
Best practices the small business / small employer has to follow
The small business / small employer concerned had better adhere to the following best practices, amongst others,
- It has to implement and maintain a program which ensures the systematic identification, evaluation, and prevention or control of general workplace hazards, specific job hazards, and potential hazards which may arise from foreseeable conditions. Towards this end, it should go beyond what the law prescribes. The emphasis should be on prevention of injuries and illnesses and not mere compliance with the law.
- Effective enforcement of the program is more important than a graphic description of the program. But in case of large worksites or worksites where complex and hazardous operations are involved, written guidance is advised. The reasons is, written guidance ensures clear communication of policies and priorities and consistent and fair application of rules.
- Management commitment and employee involvement are imperative if the program is to succeed.
- Worksite analysis should be conducted by undertaking a variety of examinations to ensure that not only existing hazards but also the conditions and operations in which changes might occur leading to new hazards, are identified. In other words, harmful occurrences should be anticipated and prevented.
- It should be ensured that hazard prevention and controls are triggered once it is determined that a hazard or potential hazard exists. Wherever possible, such hazards should be prevented by effective design of the jobsite or job. Where it is not possible, such hazards should be controlled to prevent unsafe and unhealthful exposure.
- Safety and health training should be imparted to employees while imparting training about performance requirements and job practices, depending upon the size and complexity of the worksite and the nature of the hazards and potential hazards at the site.
- In the circumstances, the small business / small employer should define a worksite policy on safe and healthful work and working conditions so that all personnel with responsibility at the site and other locations understand its importance relative to other organizational values.
Need a better understanding of OSHA regulations? Attend any of the following ComplianceOnline webinars:
|
||
- It should establish and communicate a clear goal for the program and the objectives for meeting that goal so all the members of the organization understand the results desired and the measures planned for achieving them
- The management should visibly involve itself in implementing the program to convince the rest that its commitment to the program is serious.
- Assigning and communicating responsibility for all aspects of the program will make the managers, supervisor and employees in all parts of the organization understand what is expected of them.
- To ensure that the assigned responsibilities are met, appropriate authority and resources should be provided to responsible parties.
- To ensure that essential tasks are performed, the managers, supervisors and employees concerned should be held accountable.
- Operations under the program should be reviewed at least at annual intervals to ascertain if the desired goal has been achieved and the targeted objectives have been fulfilled; simultaneously, deficiencies if any should be identified so the program can be appropriately tweaked.
- As regards worksite, all hazards should be identified by conducting comprehensive baseline worksite surveys for safety and health and periodic comprehensive update surveys.
- Planned and new facilities, processes, materials and equipment should be analyzed
- Routine job hazard analyses should be undertaken
- Regular site safety and health inspection should be provided for so new or previously missed hazards and failures in hazard controls are identified
- An analysis of injury and illness trends over time should be undertaken so patterns with common causes can be identified and prevented.
After the small business / small employer satisfies all SHARP requirements, the Consultation Project Manager in the State concerned may recommend the worksite for SHARP approval. Consequent upon approval / recognition, a SHARP certificate is issued jointly by the State and OSHA to the small business / small employer concerned.
Source:
Compliance Trainings

Pregnancy in the Workplace: Strategies to Protect Your Organization from Pregnancy Discrimination Claims
By - Christopher W. Olmsted
On Demand Access Anytime
By - Christopher W. Olmsted
On Demand Access Anytime

How to Vet an IRB: Expose and Fix Problems Before They Threaten Your Trial
By - Madhavi Diwanji
On Demand Access Anytime
By - Madhavi Diwanji
On Demand Access Anytime

Compliance Standards
Best Sellers
- Add to Cart
- Add to Cart
- Add to Cart
- Add to Cart
- Add to Cart
- Add to Cart
- Add to Cart
- Add to Cart
-
By: Miles HutchinsonAdd to CartPrice: $249
- Add to Cart
- Add to Cart
- Add to Cart
- Add to Cart
- Add to Cart
- Add to Cart
-
San Francisco, CA | Aug 6-7, 2020
-
Virtual Seminar | Jul 16-17, 2020
-
Virtual Seminar | Jun 18-19, 2020
-
Los Angeles, CA | Aug 20-21, 2020
-
Virtual Seminar | Jul 16-17, 2020
-
Virtual Seminar | Jun 25-26, 2020
-
Virtual Seminar | Jun 10, 2020
-
Virtual Seminar | Jun 3-4, 2020
-
Virtual Seminar | Jul 6-7, 2020
-
San Francisco, CA | Oct 22-23, 2020
-
Virtual Seminar | Jul 9-10, 2020
-
Virtual Seminar | Jun 3-4, 2020
-
Virtual Seminar | June 3-4, 2020
-
Miami, FL | Jul 29-31, 2020
-
Virtual Seminar | Jun 17, 2020
-
Provider: ANSIAdd to CartPrice: $142
- Add to Cart
- Add to Cart
- Add to Cart
-
Provider: ANSIAdd to CartPrice: $120
-
Provider: ANSIAdd to CartPrice: $250
-
Provider: SEPTAdd to CartPrice: $299
- Add to Cart
-
Provider: Quality-Control-PlanAdd to CartPrice: $37
- Add to Cart
-
Provider: At-PQCAdd to CartPrice: $397
- Add to Cart
- Add to Cart
- Add to Cart
- Add to Cart
You Recently Viewed
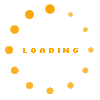