Transport and Distribution of Clinical and Commercial Products - Managing Temperature Excursions
To ensure safety and efficacy, Pharmaceutical products must meet the defined quality characteristics throughout its life-cycle. The accountability for the product's quality until its final use rests on the pharmaceutical manufacturer.
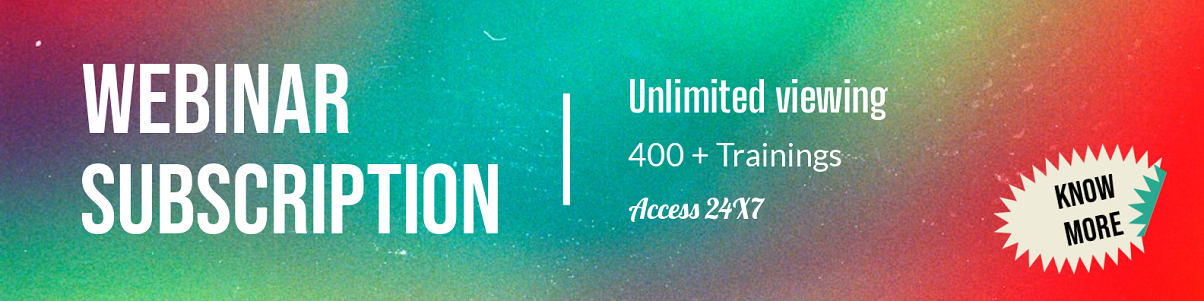
This article discusses
- The complexities in the storage and distribution of pharmaceutical products
- Obligations of manufacturers in supporting storage conditions and handling during preparation and transport
- The management of temperature excursions
Complexities in the storage and distribution of pharmaceutical products
Temperature excursion
The WHO model defines temperature excursions an "an excursion event in which a Time Temperature Sensitive Pharmaceutical Product (TTSPP) is exposed to temperatures outside the range(s) prescribed for storage and/or transport. Temperature ranges for storage and transport may be the same or different; they are determined by the product manufacturer, based on stability data"
In short, Temperature excursions occur when a Pharmaceutical Product is exposed to temperature outside the ranges prescribed for storage and transport.
Locations where Temperature excursions may occur and the causes
Temperature deviations may occur at the manufacturing site, or during transportation, or warehouse locations.
Some of the reasons for temperature excursions at manufacturing site are outlined in the following figure.
Transportation
Risks - temperature, vibration, shock, humidity, Single mode or multiple modes of transportation
Consider the complexity of the storage and distribution of pharmaceutical products - Its journey from the manufacturer's site to the patient. In its simplest form, the manufacturer may directly send the product to the doctor's office, clinic, or hospital. In its more complex form, the distribution chain may involve a number of storage and transit locations, including airports, docks, and a various means of of transport, including aircraft.
Understanding the Manufacturers Obligations in ensuring safety, efficacy, and quality of the product until its final use
The manufacturer must test the stability of the drug substances and products and define handling and transport conditions
(ICH) Q1A to Q1E, or Q5C, guidelines or guidelines, or the World Health Organization (WHO) Technical Report Series, No. 953, 2009, Annex 2, "Stability testing of active pharmaceutical ingredients and finished pharmaceutical products"
Stabillity study includes:
- Stress study to determine the drug substance's degradation path and to establish suitable analytical methods
- Drug substance stability studies to define stability under long-term and accelerated storage conditions
- The drug substance is formulated into a drug product and compatibility of the drug substance with excipients and container parts is then tested
- When suitable conditions are determined, long-term and accelerated studies commence with the drug product
- The data obtained from these studies are used to define the optimal storage conditions and corresponding retest dates for the drug substance or shelf-lives for drug product.
Guidance:
- Stability studies to support storage conditions
- Stability studies to support product handling during preparation and transport
- Studies to decide on product acceptance after temperature excursions. PDA's proposed methodologies references:
- Guidance for Temperature-Controlled Medicinal Products: Maintaining the Quality of Temperature-Sensitive
- Medicinal Products Through the Transportation Environment PDA Technical Report 39
- Last Mile: Guidance for Good Distribution Practices for Pharmaceutical Products to the End User PDA Technical Report 46
- Guidance for Good Distribution Practices (GDPs) For the Pharmaceutical Supply Chain PDA Technical Report 52
- Guidance for Industry: Stability Testing to Support Distribution of New Drug Products PDA Technical Report 53
- Risk Management for Temperature- Controlled Distribution PDA Technical Report 58
Storage conditions are defined during stability studies in accordance with the ICH/WHO guidelines.
Written procedures and records
The management of Temperature Excursions at the manufacturing site, during transportation and warehouse storage
Have a procedure in place to investigate and handle temperature excursions.
- Notify temperature excursions immediately to the responsible person
- Review temperature monitor records regularly and approve to ascertain whether an excursion may have occurred.
- Quarantine any products stored within the affected area until the outcome of the investigation is known
- Document investigations performed including outcome of the investigation
- Describe the management of the temperature excursion within a procedure
- Consult the manufacturer/marketing authorization holder to ascertain whether any possible product quality impact may result from the excursion
- If a recall may be required, Notify HPRA immediately
- Perform investigation with equal thoroughness for Excursions within freezers or fridges used for the storage of ice/chill packs for insulated shippers
- Identify corrective actions and implement them following the investigation to prevent reoccurrence
Guidance:
- Q1A(R2) - ICH
- USP General Chapter <1079> provides guidance on how to handle temperature excursions.
Training
All staff members involved in the storage and distribution of medicinal products, including delivery drivers must receive appropriate training. The training program should include a general introduction to Good Distribution Practice, a role based training, and training on relevant items contained within the guidance document. There should be a written procedure which describes the training program and training records should be retained for each employee.
Attend the webinar 'Excursion Studies to Support Transporting and Distributing Clinical and Commercial Products' to take a deep dive into the effect of environmental factors during transportation and distribution and key factors to be considered to set up temperature-cycling studies to support excursions during shipping of pharmaceutical products depending on their label storage conditions.
The speaker, Kim Huynh-Ba, has almost 25 years of experience in analytical development, project management, strategic drug development and stability sciences. Kim has held several technical and quality positions at Astra Zeneca (formerly ICI Americas), DuPont Merck, DuPont Pharmaceuticals, Bristol Myers Squibb and Wyeth Vaccines.